预测工程分析
目录
预测性工程分析
预测工程分析 (PEA) 是制造业的一种开发方法,有助于设计复杂的产品(例如,包含智能系统的产品)。它涉及新软件工具的引入、它们之间的集成以及模拟和测试过程的改进,以改善处理不同应用程序的分析团队之间的协作。这与智能报告和数据分析相结合。目标是让仿真驱动设计,预测产品行为而不是对可能出现的问题做出反应,并安装一个流程,让设计在产品交付后继续进行。
行业需求
在经典的开发方法中,制造商提供离散的产品代。在将这些产品推向市场之前,他们使用了广泛的验证和验证流程,通常是通过结合多种模拟和测试技术。但是,在查看产品如何发展时,这种方法有几个缺点。汽车工业、航空航天工业、海洋工业或任何其他机械工业的制造商都面临着类似的挑战:他们必须重新设计他们的设计方式,才能交付客户今天想要和购买的东西。
使能流程和技术
应对这些挑战正是产品开发预测工程分析方法的目标。它指的是工具部署和流程良好对齐的组合。制造商逐渐部署以下方法和技术,直到他们的组织允许并且他们的产品需要它:
部署闭环系统驱动的产品开发流程
在这种基于多学科仿真的方法中,全局设计从一开始就被视为相互交互的子系统的集合。从很早的阶段开始,所选择的架构就同时针对所有关键功能性能方面进行了虚拟测试。这些模拟使用可扩展的建模技术,因此可以在数据可用时对组件进行细化。关闭循环发生在 2 个级别:
- 与控制系统同时开发机械部件
- 包含在用产品的数据(在继续开发实际产品的情况下)
闭环系统驱动的产品开发旨在减少测试和维修。制造商实施这种方法是为了在xxx时间实现他们的设计梦想。
增加一维多物理系统仿真的使用
一维系统仿真,也称为一维 CAE 或机电一体化系统仿真,允许对多域系统进行可扩展建模。通过连接经过验证的电气、液压、气动和机械子系统(包括控制系统)的分析建模模块,整个系统以示意图的方式呈现。它可以帮助工程师预测复杂机电一体化概念设计的行为,无论是瞬态还是稳态。
制造商通常提供经过验证的库,其中包含针对不同物理域的预定义组件。或者,如果没有,专业的软件供应商可以提供它们。使用这些,工程师可以很早地进行概念预测,甚至在任何计算机辅助设计 (CAD) 几何可用之前。在后期阶段,可以调整参数。
一维系统模拟计算非常有效。组件是分析定义的,并具有输入和输出端口。因果关系是通过将一个组件的输入连接到另一个组件的输出来创建的(反之亦然)。模型可以具有不同程度的复杂性,并且随着它们的发展可以达到非常高的准确性。某些模型版本可能允许实时仿真,这在控制系统开发期间或作为内置预测功能的一部分特别有用。<
改进 3D 仿真技术
3D 仿真或 3D CAE 通常应用于比 1D 系统仿真更高级的产品开发阶段,并且可以解释 1D 模型中无法捕获的现象。这些模型可以演变成非常详细的表示,这些表示非常特定于应用程序并且计算量非常大。
3D 模拟或 3D CAE 技术在验证和确认的经典开发过程中已经必不可少,通常通过加快开发速度和避免后期更改来证明其价值。3D 模拟或 3D CAE 在预测工程分析的背景下仍然不可或缺,成为产品开发的驱动力。软件供应商通过在建模、流程和求解器方面添加新功能和提高性能,在增强方面付出了巨大的努力。虽然此类工具通常基于单个通用平台,但通常会提供解决方案包以满足某些功能或性能方面的需求,同时向应用程序垂直领域的用户提供行业知识和最佳实践。
在 1D 仿真、3D 仿真和控制工程之间建立强耦合
由于闭环系统驱动的产品开发方法需要同时开发机械系统和控制,因此 1D 仿真、3D 仿真和控制算法开发之间必须存在紧密的联系。软件供应商通过为 de:Model 在环 (MiL)、软件在环 (SiL) 和硬件在环 (HiL) 流程提供协同仿真功能来实现这一目标。
模型在环
在评估潜在架构时,一维仿真应该与控制软件模型相结合,因为电子控制单元 (ECU) 将在产品运行时实现和保持功能性能方面之间的适当平衡方面发挥关键作用。在此阶段,工程师将设计目标逐级降低为子系统和组件的精确目标。他们使用多域优化和设计权衡技术。控制需要包含在此过程中。通过将它们与 MiL 仿真中的系统模型相结合,可以验证和选择潜在的算法。
在实践中,MiL 涉及来自专用控制器建模软件的虚拟控制与多物理系统的可扩展一维模型之间的协同仿真。这为概念和策略的调查以及可控性评估提供了准确性和计算速度的正确组合。
软件在环
确定概念控制策略后,进一步开发控制软件,同时不断考虑整体全局系统功能。控制器建模软件可以生成新的嵌入式 C 代码并将其集成到可能的旧 C 代码中,以便进一步测试和改进。
在全局、全系统多域模型上使用 SiL 验证有助于预测代码集成到硬件后从浮点到定点的转换,并在代码动作需要调整到操作条件时优化增益调度。
SiL 是一个闭环仿真过程,用于在其操作环境中虚拟验证、改进和验证控制器,并包括详细的 1D 和/或 3D 仿真模型。
硬件在环
在控制开发的最后阶段,当生产代码集成到 ECU 硬件中时,工程师会使用广泛的自动化 HiL 仿真进一步验证和验证。真正的 ECU 硬件与缩小版的多域全局系统模型相结合,实时运行。这种 HiL 方法允许工程师完成前期系统和软件故障排除,以限制实际产品原型的总测试和校准时间和成本。
在 HiL 仿真期间,工程师验证最终产品的监管、安全和故障测试是否可以毫无风险地进行。如果需要,他们会调查多个 ECU 之间的交互。他们确保软件功能强大,并在任何情况下都提供高质量的功能。当用更详细的版本替换实时运行的全局系统模型时,工程师还可以在过程中包括预校准。无论如何,这些详细的模型通常都是可用的,因为控制开发与全局系统开发并行进行。
将模拟与物理测试紧密结合
从验证和确认发展到预测性工程分析意味着设计过程必须变得更加仿真驱动。物理测试仍然是该过程的关键部分,用于验证模拟结果以及测试最终原型,这在产品验收之前总是需要的。这项任务的规模将变得比以前更大,因为需要在一个可以结合多个物理方面以及控制系统的更加集成和复杂的测量系统中测试更多的条件和参数组合。
此外,同样在其他开发阶段,将测试和仿真结合在一个良好一致的过程中对于成功的预测工程分析至关重要。
提高仿真模型的真实性
模态测试或实验模态分析 (EMA) 在纯机械系统的验证和验证中已经必不可少。它是一项成熟的技术,已用于许多应用,例如结构动力学、振动声学、振动疲劳分析等,通常通过相关性分析和模型更新来改进有限元模型。然而,上下文经常是故障排除。
作为预测工程分析的一部分,模态测试必须不断发展,提供可提高仿真真实性并处理现代复杂产品的多物理性质的结果。测试必须有助于定义真实的模型参数、边界条件和载荷。除了机械参数外,还需要测量不同的量。并且测试还需要能够验证多体模型和一维多物理仿真模型。一般而言,支持模拟的全新测试能力范围(一些基于模态,一些不基于模态)变得很重要,并且在开发周期中比以前更早。
使用模拟进行更有效的测试
随着复杂产品中参数的数量及其相互作用呈爆炸式增长,测试效率至关重要,无论是在仪器方面还是在关键测试用例的定义方面。测试和模拟之间的良好一致性可以xxx减少总测试工作量并提高生产力。
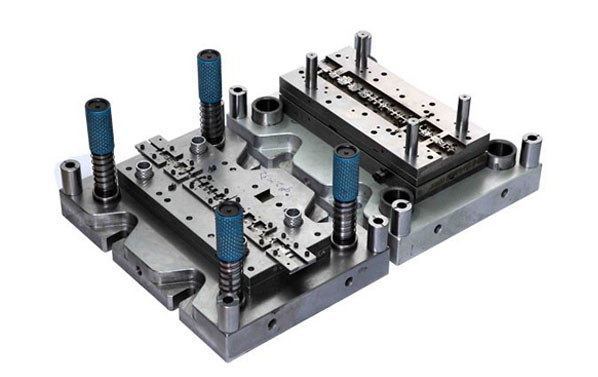
模拟可以帮助预先分析哪些位置和参数可以更有效地测量某个目标。它还允许研究某些参数之间的耦合,从而可以xxx限度地减少传感器的数量和测试条件。
最重要的是,模拟可用于导出某些无法直接测量的参数。再次,模拟和测试活动之间的紧密结合是必须的。尤其是一维仿真模型可以为大量无法直接通过传感器访问的新参数打开大门。
创建混合模型
由于复杂的产品实际上是不一定同时开发的子系统的组合,因此系统和子系统的开发需要更多的设置,包括部分硬件、部分仿真模型和部分测量输入。这些混合建模技术将允许在开发周期的早期对系统行为进行真实的实时评估。显然,这需要专门的技术作为模拟(1D 和 3D)和物理测试之间的良好一致性。
紧密集成 1D 和 3D CAE,以及在完整的产品生命周期管理流程中进行测试
明天的产品将在交付后过上生活。它们将包括基于系统模型的预测功能、适应环境、将信息反馈给设计等等。从这个角度来看,设计和工程不仅仅是将想法转化为产品。它们是贯穿整个产品价值链的数字线程的重要组成部分,从需求定义到使用的产品。
一方面关闭设计和工程之间的循环,另一方面关闭产品使用中的循环,要求所有步骤都紧密集成在产品生命周期管理软件环境中。只有这样才能实现需求、功能分析和性能验证之间的可追溯性,以及支持设计的使用数据分析。它将允许模型成为实际产品的数字双胞胎。它们保持同步,经历相同的参数变化并适应真实的操作环境。